Operation of soybean extrusion
Main process: preheat → install discharging chamber → adjust discharging screw plug → start the main motor → install the protective hood (without water add device → start feed motor, set the feeding frequency at about 10~12HZ, raise the feed rate gradually after the main motor current is decreased to ensure the stable and continuous producing.
Explanation:
——Screw down the screw plug by use of special wrench, loosen back for 3~4 circles;
——Screw down the screw upper the discharging chamber, fix the discharging screw plug;
——Start the main motor and feeding device of the extruding machine, increase feeding gradually, then install the protective hood;
——Replace the screw plug with different aperture(Φ 8, Φ 10) and adjust the position of discharging screw plug so as to get the different soybean flour output;
——The operation above mentioned should be done quickly to ensure the preheat effect.
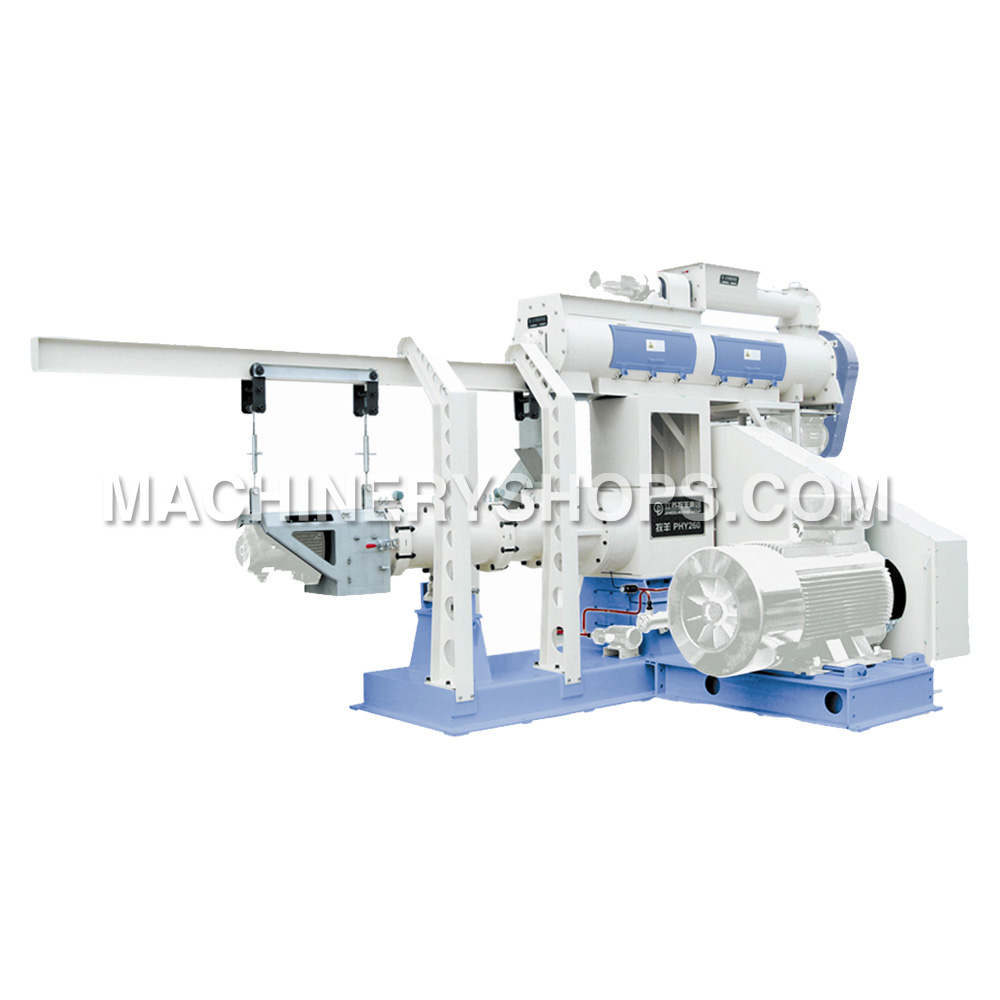
Main controls parameters under normal running (for reference)
Current of main motor 95~100A
Temperature at the discharging part 125~135℃
Operation of powdery feed extrusion
Main process: preheat → install cutting device → start main motor → start feeding device → start cutting device → adjust feeding device to normal operation state → install protective hood
Explanation:
——Fix the machine frame to avoid forward and backward movement after install the cutting device;
——Install different die and adjust cutting speed to get the material in different length and size;
——The add water volume can be set before Preheat.
Main controls parameters under normal running (for reference)
Current of main motor 90~100A
Temperature at the discharging part 110~125℃
Water pressure (select) 0.20~0.35Mpa
It is necessary to know how to operate the extruding machines, and it is also important to manage how to operate for shutdown. Close the water inlet valve first and stop feeding, and then stop the cutting device and principal machine. Remove the discharging device immediately after shutdown, clean the discharging device, after that restart the main motor, add a certain amount of soybean flour to clean away the rest material in the extruding chamber and lubricate it, so as to facilitate the next startup.