Bolt assembly type steel silo technology is the most advanced among the silo- building technologies in the modern world. Widely used in the American and European countries, bolt assembly type storage silo takes the largest market share in silo area. The modularized production avoids any human factor damages and increases accuracy, preventing damages to the zinc layer during installation. The sidewall and stiffeners are connected by detachable high strength bolts.
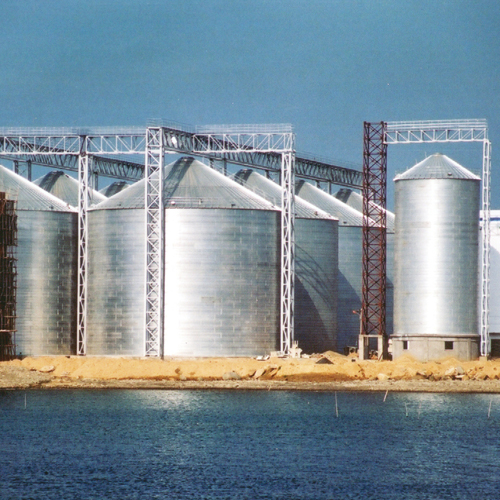
As an industrial company in large scale production of storage products, Muyang has modern workshop buildings and state-of-the-art production equipment, of which are complete production lines and technique for assembly type steel silo from USA and that from Switzerland, and silo fabricating equipment including the international first-rate YSTRONIC laser cutting machine as well.
The reason why the bolt silo is so great is that it has four distinct advantages, the first one is its large capacity, and silo roof angle is 35 degree, more storing space. Single grain silo capacity is up to 17000 tons, with comprehensive configurations to meet different customer’s requirements. It completes advanced processing equipment and technology introduced from USA to effectively ensure working accuracy and reduce damage to galvanized layer. External installable stiffeners contribute to less grain residues on silo walls. With standardized and modularized production, components and parts have a high standardization and good interchangeability, thus can be partially replaced or completely transferred.